Investing in a plastic pyrolysis plant presents both an opportunity and a challenge, as it involves considerable capital expenditure, operational complexity, and long-term sustainability. Pyrolysis is the thermal decomposition of organic materials, such as plastics, in the absence of oxygen, yielding valuable by-products like bio-oil, syngas, and carbon black. The financial potential of such a venture can be substantial, but success depends on several critical factors that must be carefully considered. This article outlines the key elements to take into account when making an investment in a plastic pyrolysis plant.
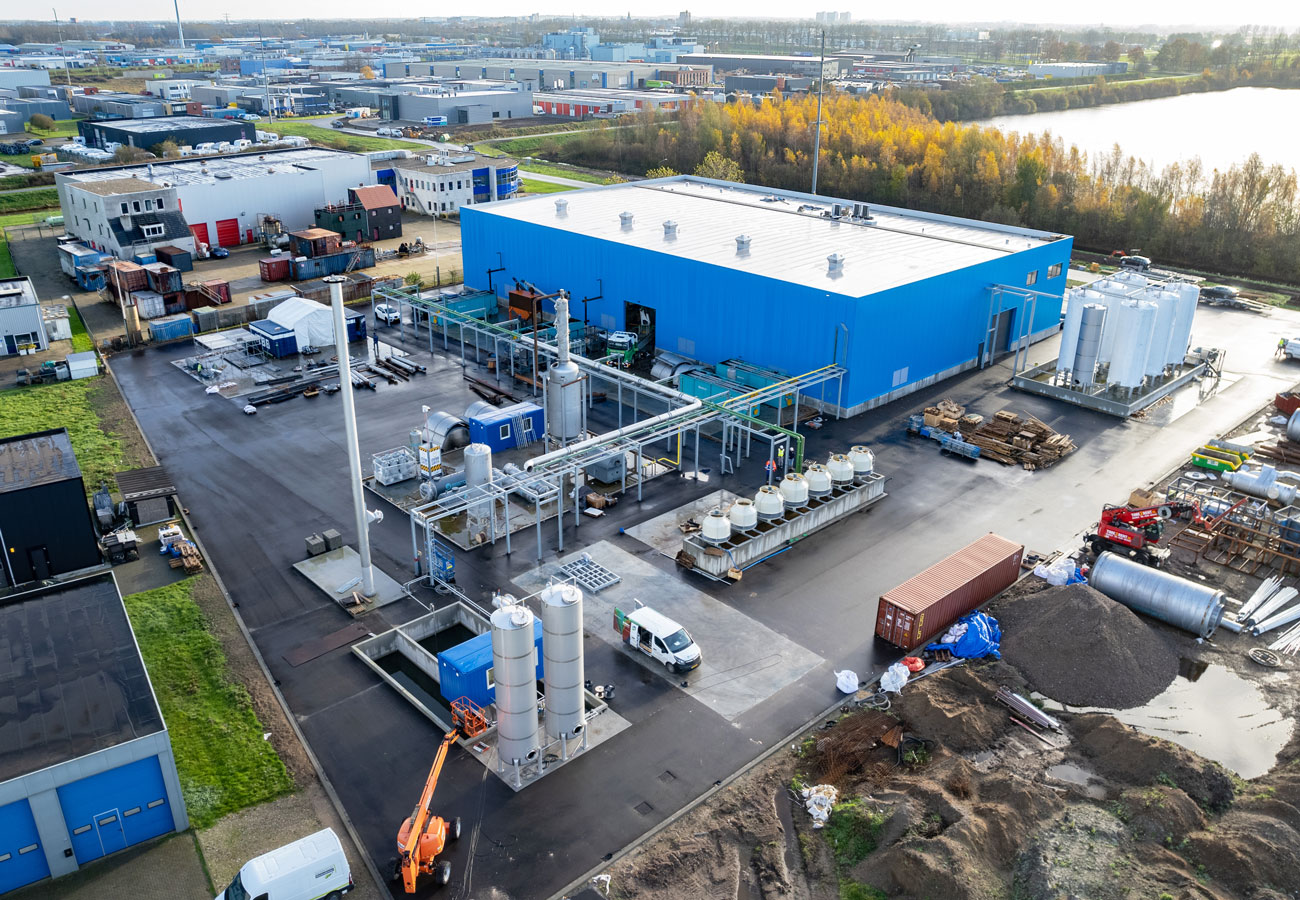
1. Initial Capital and Operational Costs
The first factor to evaluate when considering a plastic pyrolysis plant investment is the pyrolysis machine price. The cost of purchasing and installing the pyrolysis plant is a significant expense. These costs can vary depending on the plant’s size, the technology used, and the level of automation.
In addition to the purchase price, operational costs must also be factored in. These include expenses related to labor, energy consumption, and maintenance. Pyrolysis requires high temperatures, meaning that the plant’s energy efficiency is critical. If a plant is not designed to use by-products, such as syngas, for internal power generation, the energy costs can quickly escalate, affecting profitability.
Furthermore, maintenance costs should not be underestimated. Over time, equipment will require repair or replacement of components. Therefore, an understanding of the plant’s expected lifespan and potential for wear and tear is essential for forecasting long-term expenses.
2. Feedstock Availability and Quality
The profitability of a plastic to oil machine is closely linked to the availability and quality of feedstock. The type of plastic being processed can affect the yield and quality of the by-products. For instance, high-density polyethylene (HDPE) and polypropylene (PP) generally yield higher-quality bio-oil compared to more challenging plastics like polyvinyl chloride (PVC).
Before committing to a pyrolysis project, it is important to assess the feedstock supply chain. Consider whether local industries produce sufficient quantities of plastic waste or if it will be necessary to secure feedstock from distant locations, which may add to transportation costs. Additionally, the feedstock should be pre-processed to remove contaminants that can interfere with the pyrolysis process.
3. Technology and Plant Design
The technology and design of the pyrolysis plant directly influence its efficiency, output quality, and scalability. Different pyrolysis technologies are available, ranging from batch to continuous reactors. A continuous pyrolysis plant allows for higher throughput and reduces labor costs, making it more suitable for large-scale operations.
When selecting technology, it is crucial to ensure the plant can handle the specific types of plastic that will be used as feedstock. Some systems are optimized for specific materials and may require modifications to process other types of waste. Additionally, the reactor’s temperature control, pressure regulation, and gas collection system should be designed for optimal product yield and energy efficiency. Therefore, a professional pyrolysis plant manufacturer is crucial.
4. Environmental Impact and Regulatory Compliance
The environmental impact of operating a plastic pyrolysis plant must be carefully evaluated. While pyrolysis is considered an environmentally friendly alternative to landfill disposal, the process still generates emissions that need to be managed. The proper installation of gas treatment systems, such as scrubbers and filters, is essential to minimize harmful emissions and meet local environmental regulations.
Additionally, the regulatory environment governing waste management, emissions, and energy production can vary significantly by region. Investors should research the regulatory landscape in the country or region where the plant will be located to ensure compliance with laws related to emissions, waste disposal, and product certification.
Failure to comply with environmental regulations can result in heavy fines and damage to the business’s reputation, potentially jeopardizing the long-term viability of the project. If you want to choose eco-friendly equipment, you can’t go wrong with Beston Group Co., Ltd..
5. Product Marketability and Revenue Streams
The potential profitability of a plastic pyrolysis plant is also influenced by the demand for its by-products. Bio-oil, syngas, and carbon black all have established markets, but prices and demand can fluctuate depending on global economic conditions, government policies, and technological advances.
-
Bio-oil can be used as a renewable fuel source, but its quality must meet specific standards to attract buyers in the energy sector.
-
Syngas, primarily composed of hydrogen and carbon monoxide, can be utilized for electricity generation or industrial heating, though it may require further treatment to enhance its purity and energy content.
-
Carbon black is commonly used in the production of rubber, pigments, and plastics, and demand for this material depends on the performance of related industries, such as automotive manufacturing and tire production.
Before investing, conducting market research to identify reliable buyers and price trends for these by-products is crucial for ensuring the economic feasibility of the pyrolysis plant.
6. Return on Investment (ROI) and Payback Period
Finally, a comprehensive financial analysis should be conducted to assess the return on investment (ROI) and the payback period of the pyrolysis plant. This includes considering the initial capital outlay, operational costs, revenue from the sale of by-products, and potential for future scalability.
Investors should be aware that while the upfront costs can be substantial, the revenue generated from the sale of pyrolysis by-products can quickly offset these costs. A well-managed plant with consistent feedstock and efficient operation can achieve a positive ROI within a few years. However, the payback period will vary based on factors such as plant size, feedstock availability, and product demand.
7. Market Trends and Technological Advancements
Staying up-to-date with the latest market trends and technological innovations is essential for ensuring the long-term competitiveness of a plastic pyrolysis plant. Advances in pyrolysis technology can lead to better efficiencies, higher yields, and more environmentally friendly operations. Monitoring developments in feedstock processing, by-product utilization, and emissions control can provide investors with opportunities to improve their operations and reduce costs.
In addition, changes in government policies regarding waste management, plastic recycling, and renewable energy production may create favorable conditions for growth. Investors should stay informed about such changes and adapt their business strategies accordingly.