The levels of plastic wastes increase significantly from one year to the next, which has resulted in a significant environmental concern. Pyrolysis is known as a tertiary recycling process has been presented as the most current solution to this issue. It helps to reduce the plastic to diesel plant cost. Pyrolysis is either catalytical or thermal and has been used for a variety of experimental conditions.
The condition will affect the amount and the types of products that are obtained. Through the process of pyrolysis, products of high-value can be obtained like fuel oils such as diesel as well as feedstock dedicated to newer products. The promising alternative of pyrolysis allows for a conversion involving polymers into liquid hydrocarbons and gas.
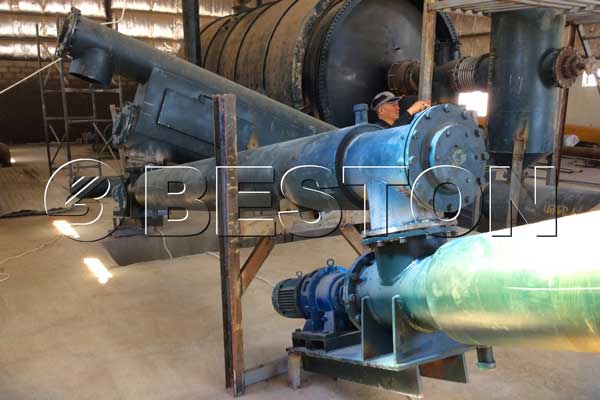
Pyrolysis is also recognized as a process that involves relatively low costs that results in a wider distribution in association to the products that are obtained. The process involves heating where there is no oxygen present, whereby organic compounds will be decomposed which generates liquid and gaseous products. The end product results in fuels of sources for other chemicals. At the same time the inorganic materials will remain unchanged and can be further recycled at a later stage. To see more details of plastic pyrolysis cost click here: https://www.bestongroup.com/waste-plastic-pyrolysis-plant/.
The process of thermal pyrolysis necessitates extremely high temperatures, which in most cases results in a product of lower quality, which has made this process unfeasible. This happens because uncatalyzed thermal degradation that results in weight substances that are low-molecular.
These methods have been improved with the introduction of catalysts, that reduce these temperatures along with the reaction times which allows for hydrocarbon production of a higher value such as petrochemical feedstocks and fuel oils. The introduction and use of these catalysts give added value in regard to the cracking efficiency and pyrolysis of the catalysts that is dependent on the physical and chemical characteristics. These properties are what break down the C-C bonds and also determine the chain lengths of products obtained.
Byproducts of Plastic to Diesel Machine
The byproducts of plastic to diesel machine for sale are usually pyrolysis oil and carbon black which are as follows,
• Plastic Oil
Also known as pyrolysis oil, this synthetic oil is useable in its raw form for the production of qualified diesel oils for use in machinery such as trains, airplanes along with other heavy-duty machines. A refinery machine for waste oils is required to extract the diesel out of this oil type.
• Charcoal
Charcoal also is known as carbon black can be produced through pyrolysis plant setup. This is also classified as a fuel type. As for the charcoal, you can use the reprocessing machine to get the better quality of it.
Pyrolysis involving plastic to diesel has been proven to be an effective method when compared to a number of other types of disposal methods, as it reuses energy and raw materials that is contained in this waste. This has resulted in a reduction on environmental impacts that are caused by the incorrect disposal of plastic waste.