Since the number of vehicles in almost all countries is increasing the number of tyres which are used is also increasing. These tyres are used for a few years after which they are get damaged or punctured and have to discard. Instead of dumping the used tires in landfills, and using up valuable space, the tyres and other similar products can be recycled to produce valuable products using a tyre to oil plant. In addition to tyre oil, the other by-products which are produced are carbon black, steel wires, and combustible gas. The design of the plant is discussed.
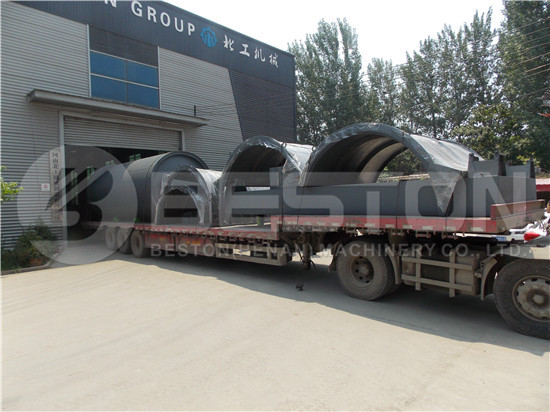
Tyre Pyrolysis Process
For processing the used tyres, they are put on a conveyor belt to move them to the different sections of the processing plant. In the first section, the tires are shredded into tyre rubber blocks in a shredder. They are then converted into smaller tyre rubber chips in the second shredder. The rubber chips are then moved to the furnace where pyrolysis of the rubber chips is taking place. The furnace is of rotary type and to ensure that proper heating of the rubber chips takes place, the reactor is filled to only two third of its capacity.
During the pyrolysis process the rubber chips are heated at a very high temperature of up to 350 degree Celsius in the absence of air. This results in the breakdown of the rubber molecules and compounds into the various ingredients. The various end products are produced from the used tyres as the temperature increases. The light oil gas will be produced at around 100 degree Celsius and the fluid oil gas will be generated at a temperature of 250 degree Celsius. This gas is collected in the manifolds of the furnace, where it is cooled in the condenser to produce the tyre oil for storage in the oil tank. The sludge in the oil is stored in the sludge oil tank. Here is a video from Beston Youtube.
Models to Choose From
Businesses interested in purchasing a plant for converting waste tyre should note that the plant design depends on the number of waste tyres which will be processed. For smaller amounts of tyres, less than 10 tonnes a day, a batch plant will be adequate. If the waste tyre available is between 10 and 20 tonnes daily, a semi-continuous plant will be feasible. For large quantities of tyres, more than 20 tonnes daily, a continuous tyre processing plant is offered by most manufacturers. The smaller plants will cost less, however, the profit generated will also be less. Beston Machinery is one of the top tyre pyrolysis plant suppliers, which will help you to get the most suitable business plan.
End Products of Tyre Pyrolysis
The other products from the pyrolysis of used tyres are fuel gas, carbon black and steel wire. The tyre oil can be distilled to remove impurities and produce gasoline or diesel. The diesel can be used for generators. The sulfur is removed from the gas which is produced using the process of desulfurisation and dust removed using de dusting. This gas can be used for heating the furnace again, reducing the energy expenses. The carbon black is used for a number of applications.
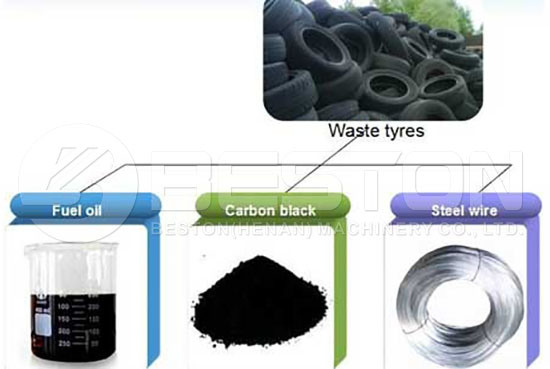
One of the main advantages of recycling the waste tyres is that there are no waste products, all the products produced after pyrolysis can be sold for profit. Hence the waste tyre recycling plant is very environmentally friendly. The carbon black can be also used to make carbon bricks. The manufacturer of the plant for processing used tyres will also install the plant at the customer site. They will train the customer on using the plant, and maximizes its output. For safety, there are temperature and pressure gauges which are installed, which will monitor the parameter and trigger alarms if required.